Mivan framework system Vs Conventional method of construction.
Read latest blogs and articles from Housystan
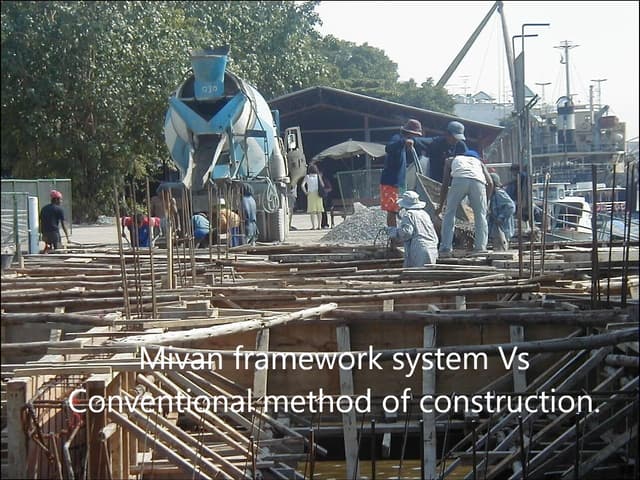
The Information mentioned here was last updated on:
12/8/2025When it comes to building strong and reliable structures, the choice between the Mivan framework system and the conventional method of construction often sparks a lively discussion among builders, engineers, and homeowners. Each method brings unique advantages to the table, especially in today’s fast-paced real estate and infrastructure development landscape in India and across the world. Let’s dive into how the Mivan framework system compares to the traditional construction methods, and what this means for anyone interested in modern building techniques, cost-effective housing, durability, and speedy project completion.
First, let’s talk about what makes the Mivan framework system so different. The Mivan technology uses aluminum formwork to create a precise mold for concrete walls and slabs. This technique is popular for high-rise buildings, affordable housing projects, and large-scale developments where speed and efficiency are essential. Using this system, both walls and slabs are cast together in a single pour, which greatly reduces the time needed for construction. Compared to the conventional method, which usually relies on brick masonry and concrete columns, the Mivan framework system stands out for its uniformity and structural strength.
One of the top construction keywords today is “speed of construction,” and Mivan technology really shines in this area. Since the formwork can be quickly assembled and reused multiple times, builders can finish projects much faster than with traditional techniques. This is especially useful in mass housing projects where thousands of homes need to be delivered within tight deadlines. The conventional method, on the other hand, is labor-intensive and requires more time for bricklaying, curing, and finishing, which can slow down the entire process.
- Verified Tenants/Buyers
- Unlimited Property Listing
- Zero subscription/charges fee
Durability is another important keyword in modern construction. Structures built using the Mivan system are known for their monolithic strength, as the walls and slabs form a single, continuous unit. This means fewer joints, less seepage, and a longer lifespan for the building. In contrast, conventional construction methods may face challenges like cracks and water leakage at the joints, which can affect the life and maintenance costs of the building in the long run.
When it comes to quality, the Mivan framework ensures a smooth finish for both exterior and interior surfaces, reducing the need for extra plastering or finishing work. This not only helps in achieving a premium look but also saves time and material costs. In the conventional method, achieving a similar level of finish often requires more work and skilled labor, which can increase the overall project cost.
Let’s not forget about cost-effectiveness—a keyword that’s always on the minds of builders and property buyers. While the initial investment in Mivan technology is higher due to the cost of the aluminum formwork, the ability to reuse the formwork across multiple projects, combined with faster completion and reduced labor costs, often balances out the expenses. On the other hand, the conventional method might seem cheaper at first but could lead to higher costs over time due to longer construction periods and more frequent maintenance needs.
Safety, sustainability, and energy efficiency are also gaining attention in the construction world. The Mivan system reduces material wastage, minimizes human error, and promotes a safer site environment because of its organized process. Traditional methods, meanwhile, can produce more debris and require more manual handling, which may impact both safety and sustainability efforts.
So, whether you’re a builder, architect, or someone planning to invest in real estate, understanding the differences between the Mivan framework system and conventional construction methods can help you make better choices for your next project. Which method do you think suits your needs—speedy, modern, and precise Mivan construction or the tried-and-tested conventional approach? The construction industry is evolving, and the right choice could make a world of difference in your next building adventure!